To improve the durability of
high strength bolt in various applications, it's essential to implement a combination of preventive measures and maintenance practices. Here are some strategies to enhance the durability of high-strength bolts:
Select Corrosion-Resistant Materials: Choose high-strength bolts made from materials known for their corrosion resistance, such as stainless steel or weathering steel. These materials are less susceptible to corrosion and can significantly improve durability.
Use Corrosion-Resistant Coatings: Apply durable and well-adhering corrosion-resistant coatings, such as hot-dip galvanizing or epoxy coatings, to the surface of the bolts. These coatings act as a protective barrier against environmental factors.
Proper Coating Thickness: Ensure that the applied coatings have the correct thickness to provide effective protection. Follow manufacturer guidelines for coating thickness, and monitor and maintain the coatings over time.
Regular Inspections: Implement a regular inspection program to assess the condition of the bolts. Look for signs of corrosion, coating damage, or any degradation. Early detection allows for timely maintenance.
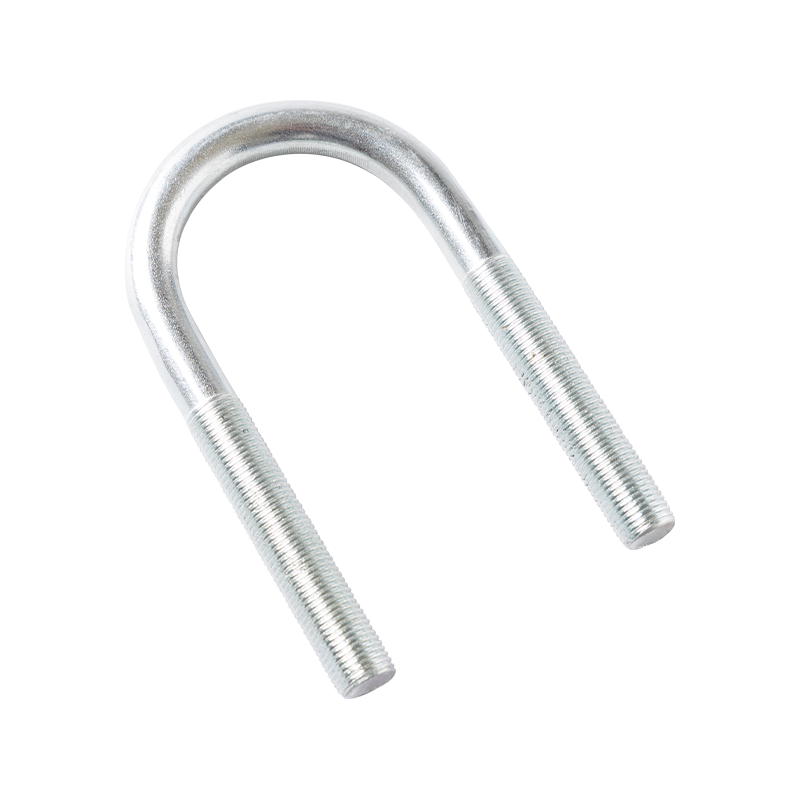
Scheduled Maintenance: Develop and adhere to a maintenance schedule that includes periodic cleaning, reapplication of coatings (as needed), and visual inspections of the bolts. Ensure that maintenance activities are conducted at recommended intervals.
Cathodic Protection: In highly corrosive environments, consider using cathodic protection systems, which involve sacrificial anodes or impressed current systems to protect the bolts from corrosion.
Environmental Controls: Implement measures to shield bolted connections from harsh environmental conditions. This can include enclosures, barriers, or sheltering the connections from corrosive agents.
Bolt Lubrication: Apply lubricants or anti-seize compounds during installation to prevent galling and corrosion between bolt threads and the mating threads of nuts or other components. Ensure the lubricants are suitable for the application's environmental conditions.
Tightening Procedures: Follow recommended installation procedures and torque specifications to ensure that the bolts are properly tensioned and securely fastened. Avoid under-tightening, which can lead to loosening, and over-tightening, which can damage the bolts.
Environmental Considerations: Account for specific environmental factors, such as humidity levels, temperature variations, and exposure to chemicals or corrosive substances, when designing bolted connections. These factors can significantly impact durability.
Use Thread Lockers: Consider using thread-locking compounds designed to prevent vibration-induced loosening of bolts, especially in applications subjected to dynamic loads.
Prevent Contamination: Keep the bolted connections clean and free of debris, chemicals, or other contaminants that can accelerate corrosion or degrade coatings.
Regular Torque Checks: Periodically check the torque of high-strength bolts in critical applications. This ensures that they maintain the desired preload and stay properly tensioned.
Compliance with Standards: Adhere to industry standards and codes that specify requirements for bolt selection, installation, and maintenance in various applications. These standards provide guidelines for ensuring safety and durability.
Material Compatibility: Ensure that all components in the bolted connection are compatible with one another in terms of materials and coatings. Incompatibility can lead to premature degradation.
Improving the durability of high-strength bolts requires a proactive approach that includes material selection, proper installation, regular inspections, and a well-planned maintenance program. By taking these measures, you can extend the lifespan of bolted connections and ensure their reliability in a wide range of applications.