Inspecting
high strength bolt for damage or fatigue typically involves visual inspection and, in some cases, non-destructive testing methods. Here are some common techniques used to inspect high-strength bolts:
Visual Inspection: Start by visually examining the bolt and its surrounding area for any visible signs of damage, such as cracks, deformation, corrosion, or loose threads. Look for any indications of stress concentration points or evidence of previous overloading. Pay attention to the bolt's head, shank, and threaded regions.
Ultrasonic Testing (UT): Ultrasonic testing uses high-frequency sound waves to detect internal flaws or defects in materials. It can be used to inspect the entire bolt or specific critical areas. UT can identify cracks, voids, or other anomalies that are not visible to the naked eye.
Magnetic Particle Inspection (MPI): MPI is a technique used to detect surface and near-surface defects in ferromagnetic materials. It involves applying a magnetic field to the bolt and then applying a magnetic particle solution. Any defects or cracks will create magnetic flux leakage, which can be visualized by the accumulation of the magnetic particles.
Dye Penetrant Inspection (DPI): DPI is a method used to locate surface-breaking defects in materials. It involves applying a liquid dye to the bolt's surface and allowing it to penetrate into any surface cracks or defects. After a specific time, excess dye is removed, and a developer is applied to make the indications visible.
Radiographic Testing (RT): Radiographic testing, commonly known as X-ray inspection, uses X-rays or gamma rays to examine the internal structure of the bolt. This method can detect internal defects, such as voids or cracks, but requires specialized equipment and expertise.
Load Testing: In some cases, load testing may be performed to evaluate the integrity and performance of high-strength bolts. This involves subjecting the bolt to a known load to assess its behavior and identify any signs of deformation or failure. Load testing should be conducted by experienced professionals using appropriate equipment and safety measures.
ProductNon-standard punched J bolts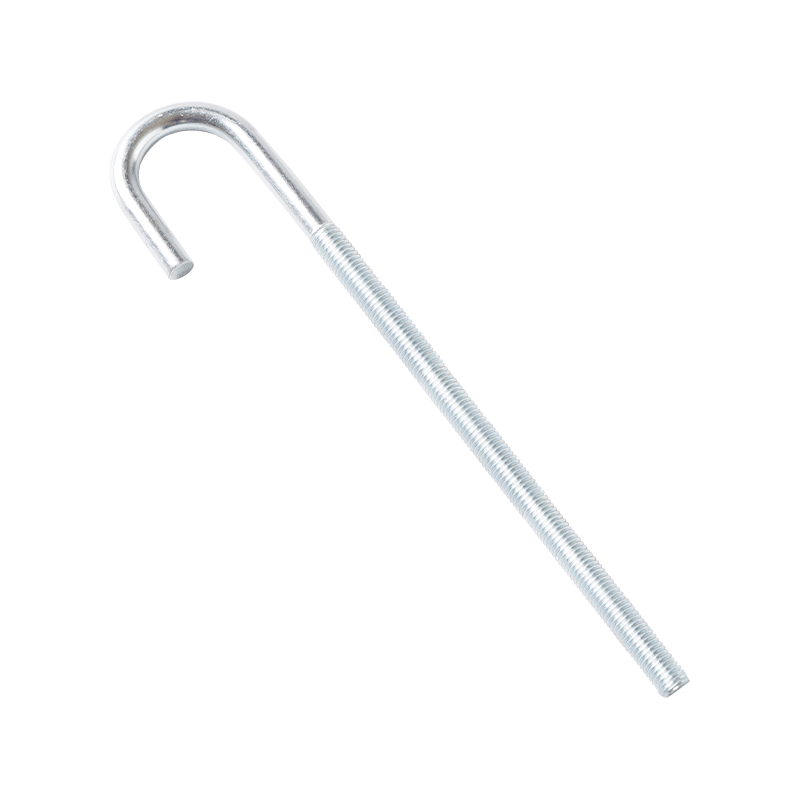
Can be customized according to customer drawings are non-standard. Latching and fastening options are available primarily for indoor and outdoor applications. Barrel, Dutch door, flush, tongue and groove and surface bolts are designed with ease of use and security in mind. The surface can be made of blue and white zinc color zinc hot dip galvanized dacro electrophoretic paint, zinc plating provides corrosion resistance for all your functional hardware needs.